Salida a las 8:00AM desde el Aparcamiento de Plasencia, que se ubica en la Avenida del Valle nº20.
Visita 6: Alcornocales e industria del corcho
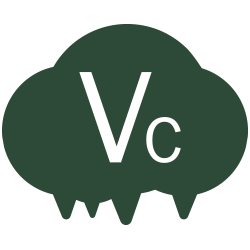
Viaje de campo
Viaje de campo
Esta ruta, como su denominación indica, está destinada al estudio del alcornocal y al de la transformación industrial del corcho.
Por la mañana visitaremos un monte público Valcorchero y en dónde nos espera un almuerzo. En el desplazamiento hacia San Vicente de Alcántara tendremos ocasión de parar en los riberos del Alagón, que por su riqueza en flora y fauna mediterráneas se hallan declarados LIC y ZEPA junto con los Canchos de Ramiro, espectacular portilla cuarcítica en la desembocadura del Alagón en el Tajo. Siguiendo nuestra ruta atravesaremos el Tajo por el puente de Alcántara, una de las joyas arqueológicas de la época romana en Extremadura. Y ya por la tarde, tras la comida, visitaremos la localidad de San Vicente de Alcántara, uno de los principales polos de la industria corchera en el mundo. Durante el regreso a Plasencia tendremos la ocasión de atravesar el corazón de Sierra de San Pedro, un espacio natural protegido que produce una buena parte del corcho de Extremadura, y además de una calidad excepcional.
Responsable de ruta: Ramón Santiago Beltrán (Instituto del Corcho, la Madera y el Carbón Vegetal del CICYTEX).
PROGRAMA
HORARIO | DESCRIPCIÓN |
---|---|
8:00 AM | Salida desde el aparcamiento de la Av. del Valle, 20. |
8:30 AM | PARADA 1. Monte Público "Valcorchero". |
14:00 AM | Comida en San Vicente de Alcántara. |
3:30 PM | PARADA 2. EXTRACOR AVA S.L. |
4:30 PM | PARADA 3. DIAM CORCHOS S.A. |
8:00 PM | Llegada estimada al casco urbano de Plasencia. |
Responsables de la parada: Raúl Lanzo Palacios y Ramón Santiago Beltrán Instituto (CMC-CYCYTEX).
El Monte Público "Valcorchero" pertenece al Ayuntamiento de Plasencia, y donde el uso recreativo se compatibiliza con los aprovechamientos ganadero y corchero. Durante la visita tendremos ocasión de ver el Plan de Calas de IPROCOR, un descorche tradicional y un descorche con nuevas tecnologías.
Plan de Calas de IPROCOR.
El objetivo del Plan de Calas de IPROCOR es establecer la calidad de corcho de una partida comercial, mediante un muestreo forestal durante el cual se toman 75 muestras de corcho, y un escogido posterior de estas muestras. Una vez muestreados los 75 árboles, se pueden tomar datos del conjunto de la explotación: carga ganadera, valoración de la selvicultira practicada, datos de la vegetación, datos de la masa (densidades, altura dominante,...). Las muestras de corcho se trasladan al laboratorio de calidad de corcho del CICYTEX, y allí sufren un proceso similar al que se realiza en la industria preparadora de corcho: Se secan en estufa, se cuecen en agua hirviendo, se dejan enjugar, se recortan y se clasifican. Los datos de calidad de corcho obtenidos de la clasificación se vuelcan a un ordenador, y mediante una hoja de cálculo específica, se realiza un informe sobre la calidad de corcho, donde se ofrecen las principales cuestiones con respecto a la calidad de corcho: porcentajes de corcho de las diferentes clases, índice de calidad Q, calibres, alteraciones del corcho, comparación de la calidad de la partida con las calidades medias de la zona y de la región. Además se indican las fortalezas y debilidades de la partida de corcho de cara a su compraventa, y una serie de recomendaciones específicas y generales para mejorar la calidad del corcho de ese alcornocal a medio y largo plazo.
Descorche tradicional.
La saca tradicional se realiza fundamentalmente con la ayuda del hacha corchera, que es un hacha peculiar, adaptada al trabajo de descorche de abrir y trazar, que consisten en realizar una serie de cortes verticales y horizontales sobre el corcho; ahuecar, que es golpear con la parte posterior del hacha en los cortes realizados previamente; dislocar, que es comenzar el desprendimiento de las planchas entre sí y de la capa madre; y separar, que es desprender completamente las planchas del árbol, y mediante un procedimiento que tiene numerosas pautas regladas.
Una vez descorchados los árboles se procede al desembosque del corcho (rodear la corcha), mediante bestias o tractores, y en los sitios más abruptos a hombros de los sacadores. La práctica tradicional es que el corcho se reúna en un lugar preparado al efecto, y se forme una pila que permanece durante 8 días intacta a fin de que el corcho se oree. Al cabo de este tiempo el corcho se pesa con ayuda de una cabria y una romana, antes de ser transportado a la industria preparadora.
Aunque poco a poco se va imponiendo el sistema métrico decimal, el mundo del corcho tiene sus propias unidades: la unidad de peso se denomina quintal castellano, y equivale aproximadamente a 46 Kg. La unidad de calibre (espesor del corcho) se denomina línea, y equivale aproximadamente a 2,25 mm.
Descorche con nuevas tecnologías
Desde hace 20 años han aparecido en el mercado un puñado de máquinas para el descorche. Todas estas máquinas realizan un corte en el corcho, determinando de forma automática la profundidad de corte para no dañar la capa madre (operaciones de abrir y trazar). Por otro lado el sector cuenta con las herramientas diseñadas en el Instituto CMC - CICYTEX para completar el trabajo de las máquinas. Estas herramientas sustituyen al hacha corchera y permiten realizar el descorche con mayor seguridad para el trabajador y con menos daños al árbol (operaciones de ahuecar, dislocar y separar).
Comida en San Vicente de Alcántara.
Responsable de la parada: Antonio Rodríguez (EXTRACOR).
La industria preparadora es la que está en contacto directamente con el corcho crudo, tal y como viene del campo y a través de un proceso industrial no excesivamente complejo, lo transforma en corcho preparado, del que se surte la industria taponera y otras.
El transporte se realiza a la fábrica normalmente en camiones, y allí se almacena en el patio donde se somete a un periodo de estabilización de al menos 6 meses, en el cual el corcho mejora sus aptitudes taponeras. Después se realiza el primer cocido, en el que el corcho es hervido en agua limpia a una temperatura próxima a 100 ºC durante una hora. A continuación, el corcho se somete a un periodo de reposo de 1 a 4 semanas en un lugar cubierto hasta que su humedad disminuye por debajo del 16%. En este momento se realiza la operación de escogido, mediante la cual se clasifican las planchas de corcho en los distintos tipos de corcho de los que se aprovisiona la industria de segunda transformación: esta clasificación se hace por calibres y por aspecto visual, y por el momento únicamente es posible realizarla de forma manual.
Las planchas clasificadas se almacenan durante un corto periodo hasta que su humedad está por debajo del 14% Y se suelen agrupar en fardos cuyas dimensiones aproximadas son del orden de 1.15 x 0.60 x 0.60 m y su peso aproximado de 80 Kg. Estos fardos son tradicionalmente la unidad de comercialización.
Responsable de la visita: Joaquín Herreros de Tejada (DIAM CORCHOS).
DIAM CORCHOS fabrica tapones tecnológicos de corcho aglomerado. Para llegar al producto final se realizan 2 tipos de actividades: fabricación de granulados de corcho y fabricación de tapones aglomerados.
Proceso general de fabricación de granulados de corcho. El primer proceso es la recepción y control de materia prima, que es de una importancia crucial para poder fabricar tapones aglomerados de calidad. La industria de fabricación de granulados se suele aprovisionar de refugo (corcho no apto para fabricación de tapones naturales) y de subproductos de la industria taponera. En segundo lugar se procede a su almacenamiento, controlando perfectamente su humedad para evitar problemas sensoriales. La tercera operación es la trituración, donde se procede al molido y despedazamiento del corcho en los molinos rompedores. A continuación tiene lugar la granulación, donde se fragmenta el corcho procedente de la trituración mediante molinos de piedras, obteniendo gránulos de un tamaño comprendido entre 0,25 y 8 mm. Luego se pasan estos granulados por las mesas densimétricas, para separarlos por densidades en función del tipo de tapón que se quiera fabricar. Los distintos tipos de granulados se someten a un secado para que su humedad no supere el 8%. Una vez secos pasan a ser almacenados, en silos o en sacas de material adecuado, hasta su venta o procesado posterior en función del tipo de empresa.
Fabricación de tapones aglomerados. El primer proceso es el control de recepción del granulado. Se controla la granulometría, que debe estar comprendida entre 0,25 y 8 mm; el peso específico, que debe ser inferior a 75 kg/m3; y la humedad, que no debe sobrepasar el 8% y se almacena en silos o sacas de material sintético que permitan su aireación. El siguiente paso es mejorar las cualidades sensoriales del granulado, eliminando los compuestos volátiles no deseados. Luego se procede al proceso de aglomeración, en el que se aglutina el granulado de corcho con ligantes y aditivos. Acto seguido se realiza el moldeo, con polimerización en caliente en moldes adecuados. A continuación se procede a la rectificación dimensional y biselado para conseguir las dimensiones especificadas. Luego se procede al escogido para eliminar los tapones con defectos; y se almacenan estos tapones, que se denominan semi-elaborados, en condiciones adecuadas para conservar sus características. Por último se cuentan y embalan para que su transporte sea óptimo. En muchas ocasiones la siguiente fase, el semiacabado, se suele hacer en otra unidad fabril.